The Role of Rotational Molding in Scalable Manufacturing Solutions
Rotomolding, also referred to in the industry as the term "rotational Molding, is a plethora of manufacturing processes that has revolutionized the creation of hollow plastic products. This process combines precision, efficiency, and creative adaptability, making it a preferred choice in industries ranging from automotive to healthcare. Let's look at why rotational molding is considered the standard of excellence for making hollow plastic products.

The Precision Behind Rotational Molding
In essence the concept of rotational molding is a process that is driven by precision. In contrast to other methods of manufacturing that start with liquid or powdered plastic material that is inserted into a hollow mold. The mold is then subjected to heating and rotating along two perpendicular axes. It is controlled to melt the substance while it evenly coats internal parts of the mold. By the time it has cooled and solidified the result is a smooth, strong, and hollow plastic product without any weak points.
One of the most notable advantages of rotational molding is its accuracy in making complex geometries. Intricate designs or uniform Wall thicknesses, this technique achieves high-quality results while reducing waste of materials.
Trending Applications of Rotational Molding
Rotational molding continues to gain traction, proving its relevance across a variety of industries. Here's how it stands as a trend-setter:
Automotive Industry: Air ducts, tanks for fuel as well as wheel arches, are typically crafted using rotational molding for their toughness and lightweightness.
Healthcare Equipment A variety of medical-grade containers and devices are perfect examples of the precision made possible by rotomolding.
Consumer Goods: Water tanks, kayaks, playground equipment and furniture are other popular applications where durability meets design creativity.
Sustainability is a major aspect of manufacturing, rotational molding allows recycling of materials efficiently, highlighting its green potential.
Why Rotational Molding Stands Out
Rotomolding provides industry professionals with a strategic edge because it can make seamless, high-quality items using minimal materials. Its cost-effectiveness in producing small, medium, or even large quantities is a major draw to manufacturers. Furthermore, the long-lasting life of products made from rotomolded materials means less maintenance costs for the customers and a boost in their popularity in highly competitive markets.
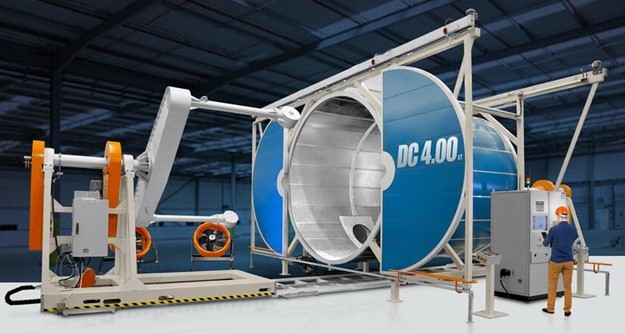
Rotational molding will definitely remain a forefront player in plastic manufacturing due to its flexibility, precision and alignment with modern industrial needs. Businesses looking for efficient solutions to high-quality and long-lasting hollow plastic products can benefit from this process to keep ahead of the trends.