Exploring the Growing Demand for Rotational Molding in Manufacturing
Rotational molding, commonly known in the industry as Rotational Molding has revolutionized way industries create robust and durable plastic products. From water tanks that are durable to intricately designed custom-made parts, rotomolding has proven its worth as a top manufacturing method for versatility and quality. But what exactly makes it so effective? Let's take a look at the process, its benefits, and the impact it has on various industries.
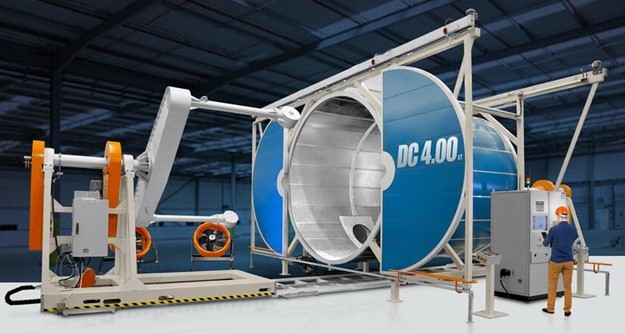
The Rotomolding Process
Rotomolding is a straightforward but extremely precise process. First, powdered plastic resin is poured into a mold. The closed mold is then turned around two perpendicular axes in an oven. Its heat instantly melts plastic powder, which ensures even distribution across the mold's surface. Once the product is fully formed, it is then cooled then solidified before being removed from the mold ready to be used.
This process allows for unparalleled design flexibility, allowing manufacturers to make products that have intricate designs with uniform wall thicknesses and high levels of durability. It is especially useful when it comes to large hollow structures, which might not be feasible using other manufacturing methods.
Why Rotomolding is a Game-Changer
Rotomolding stands out for several main reasons:
Durability The products made by the process of rotomolding have exceptional durability and can withstand tough environmental conditions, which makes them ideal for industrial and outdoor usage.
Cost-Effectiveness The molds that are that are used for rotational molding are relatively inexpensive as compared to the molds used in injection or blow molding which makes it a cost-effective choice for both large and tiny production batches.
Customization: The ability to create intricate designs and varied sizes ensures that products can be tailored to meet the specific needs of each customer.
Low Waste Rotomolding is innately efficient, using material to its maximum extent and with minimal waste, supporting sustainable manufacturing practices.
Applications Across Industries
Rotomolding forms the basis of numerous industries, assisting in the production of outdoor furniture, storage tanks playground equipment, automobile parts, and even marine products such as kayaks. Its versatility and adaptability to a variety of types of materials, such as UV-stabilized resins make it the ideal option for products that are that are exposed to different conditions.

Through its blend of durability, precision and cost-efficiency, rotomolding continues to define modern manufacturing. It's not a surprise that this technique is recognized as a sustainable and dependable method that is shaping the future of durable plastic products.